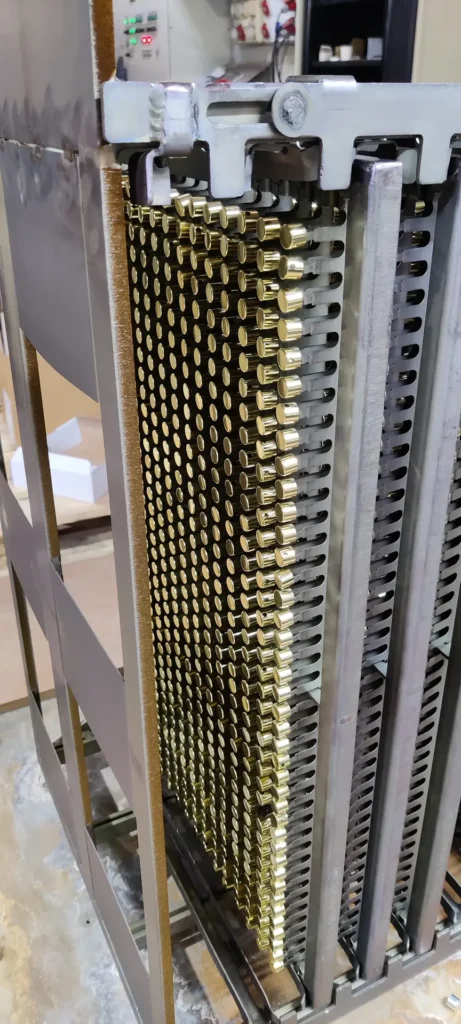
Thomas Cosmetica de Espana is a company of the globally operating Thomas Group. Their Valencia site manufactures components from tinplate and aluminium for the cosmetic industry, such as cases and caps for lipsticks or mascara. They require drying after surface finishing. Cases and caps are components liable to water entrapment. The components are positioned on their carriers such that they leave the last rinse with some water entrapped. The manufacturer has now found a process meeting all their requirements – heat pump based condensation drying. South Germany based drying system manufacturer Harter developed this low temperature drying method more than 30 years ago. This alternative drying technique dries within defined temperature limits of 40 °C to 75 °C. This is a closed air system ensuring quick, reliable and exhaust-air-free drying. Exhaust-air-free means that there is almost no emission and little carbon dioxide – an ecological and financial relief. The core of each dryer is its efficient and energy-saving heat pump system. It may be integrated in any dryer type – rack and bulk material dryers or continuous dryers. For components with complex geometries liable to very high water entrapment, Harter integrates an additional air blow-off provision to remove water before drying proper. The blow-off station uses non-compressed air.
Thomas Cosmetica already had a Harter rack dryer in operation. The drying parameters had been determined by tests in Harter’s pilot plant station. Based on these test results, the aluminium specialist installed two rack dryers of this type in their new processing line. Attached to these dryers is a so-called heat pump module which conditions the required process air and is also responsible for the condensation process. The dryers feature a special air recirculation system. The process air routeing inside the dryer is also important to ensure proper dehumidification. Thomas Cosmetica has waste heat from hot water available. This waste heat is obtained from a separate process. Such waste heat is frequently released into the environment. Thomas uses the waste heat to help the dryer auxiliary heater boost process air heating upon process run-up. This saves the manufacturer even more money. The rack dryers feature an automatic lid system which opens only for entering or removing the product carrier. The precious heat is thus retained in the system. Thomas selects a temperature between 60 °C and 75 °C, as appropriate for the specific product, to dry their cosmetic accessories. The aluminium components are completely dry and stain-free after 14 minutes. The rated power of the complete system is about 27.1 kW.