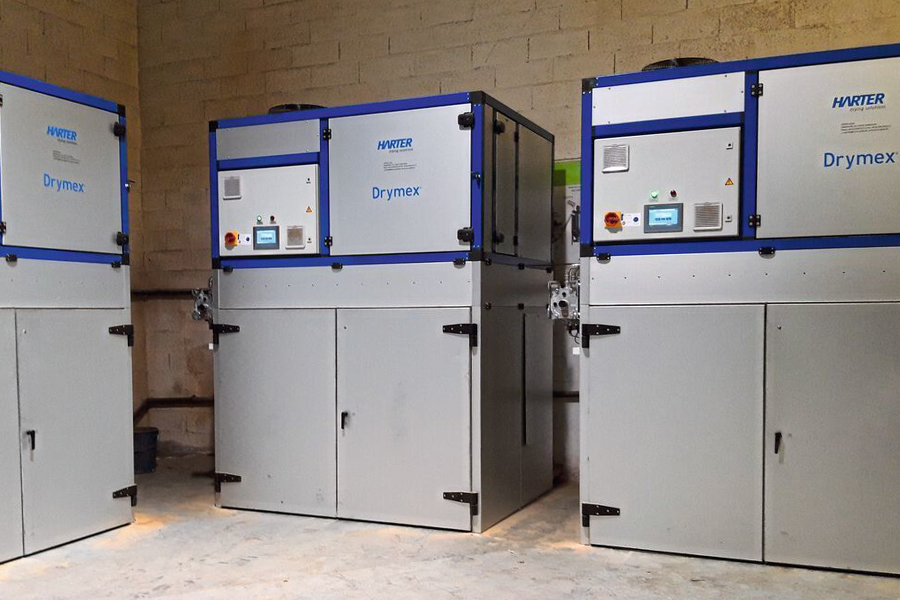
Three sludge dryers type M5 for drying a total of 3.6 t of sludge per working day.
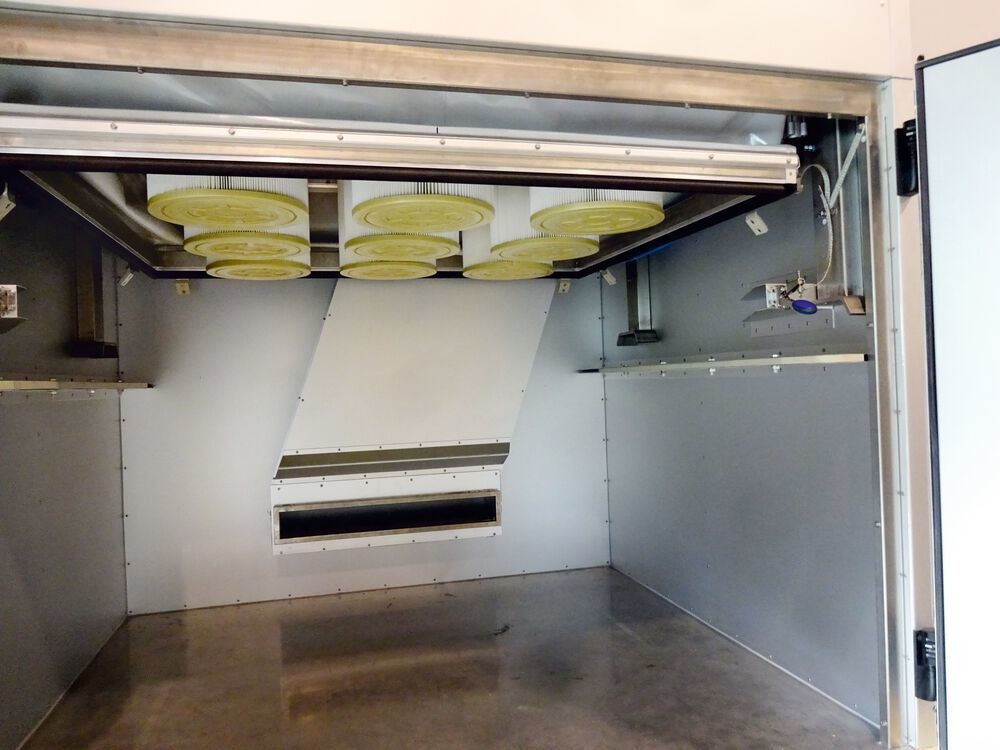
A sealing bonnet with nine special filter cartridges completely seals the sludge trolley during drying to keep the system’s heat exchangers clean.
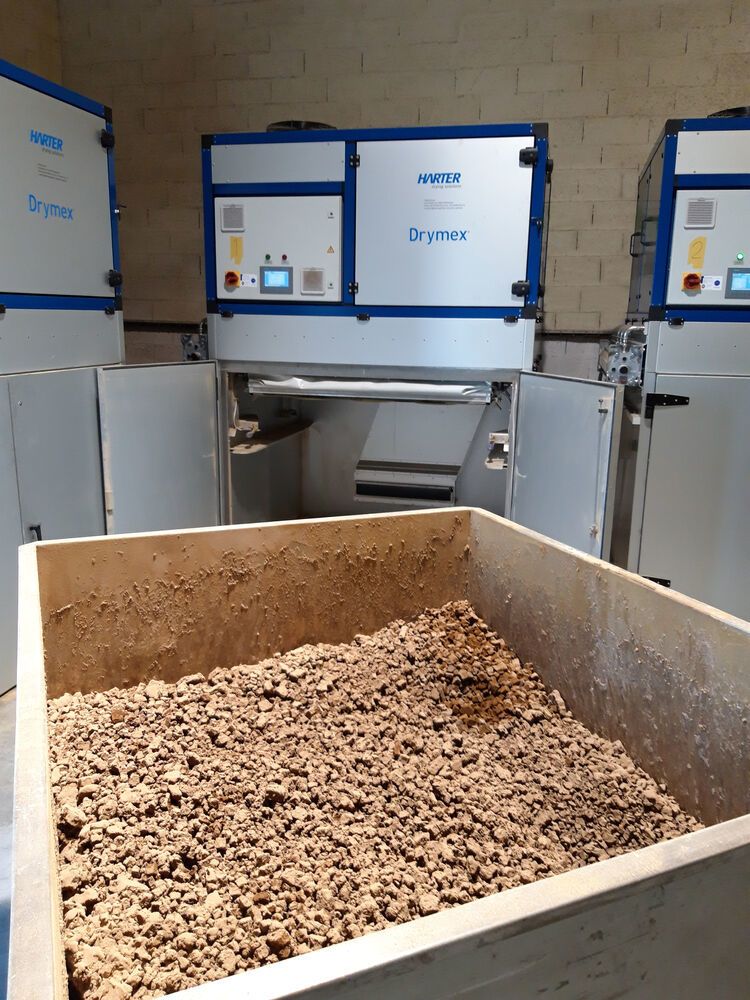
The thin sludge waits to be dried in the sludge truck.
The drier the sludge, the lower the energy consumption for processing metals from battery sludge. A simple calculation that makes a newly developed drying plant based on the heat pump principle a piggy bank for a recycling company. With the heat pump principle, the operator dries the thin sludge with low dust and efficiently to boot.
Without batteries and accumulators, there would be no mobile phones, no e-cars and no e-bikes. But what happens to the power packs when they have breathed their last? In the past, they often ended up in the rubbish, but since there is a recycling law, the recycling rates have risen and batteries have become a raw material from which some of the valuable metals are wrested again. Analysts at Markets and Markets estimate that the battery recycling market will grow by 6.1 per cent annually from 2020 to 2025, from a total of $17.2 billion in 2020 to $23.2 billion by 2025. An exciting field, then, with a handful of specialists from around the world.
Specialists in battery recycling
These include Umicore in Belgium, Glencore in Canada and Euro-Dieuze Industrie (EDI). The Veolia subsidiary from France specialises in recycling batteries from household appliances and for electric vehicle drives. Every year, 6000 batteries with an increasing share of electric car batteries are collected at the site in France, shredded, the recyclables extracted and returned to the material cycle. This process produces 1000 tonnes of thin sludge per year, which has to be dried in order to extract the sought-after metals and rare earths. The Veolia subsidiary is particularly interested in nickel and has developed a hydrometallurgical process to treat the batteries.
Sludge drying reduces disposal costs
Sludge drying is usually used because companies want to minimise their disposal and transport costs. By removing water, the weight and volume of the sludge is reduced by up to 60 percent. This can reduce landfill costs by up to 60 per cent. Harter, a drying system manufacturer from the Allgäu region of Germany, introduced a particularly energy-saving sludge drying system to the market almost 30 years ago, which still serves a gap in the market today. An interesting cost calculation for many a company.
At EDI, the starting position was different because of the recycling process. The process produces metal hydroxide sludge that is dewatered in chamber filter presses. What remains is a filter cake that still has a residual moisture content of 70 percent. To be able to extract the nickel from the sludge, a residual moisture of only eight percent is required, which makes sludge drying necessary. A challenge for the project team at Harter: for the first time, the drying specialist was faced with the requirement for such a low residual moisture. As a rule, operators dry their sludge only up to about 75 per cent residual moisture. In this range, the highest volume and weight reductions are achieved. Further drying is no longer economical.
Additional dedusting in the dryer
What does the EDI requirement mean for the construction of the plant? The dryer manufacturer was aware that from a residual moisture of approx. 25 percent, an increasingly strong dust formation sets in. The filters normally used in a sludge dryer would no longer suffice here. The heat exchangers in the plant would become dirty, which would ultimately lead to a loss of performance. To avoid this, Harter developed its own dedusting unit for the project at EDI.
Sludge drying unit consists of a sludge trolley and a dehumidification unit. The filter cake is unloaded from the filter press into the trolley and dried there. In the dehumidification unit, the required process air is prepared: extremely dry air.
This unsaturated air is fed into the sludge trolley via insulated air ducts and absorbs the moisture there. The trolley is equipped with a special aeration floor and the air flow is designed so that the dry process air flows evenly from below through the filter cake and dries it gradually.
The air enriched with moisture goes back into the dehumidification unit. There it is cooled, the water condenses out and leaves the unit as condensate. The air is then reheated and circulated further. This „condensation drying with heat pump“ is the only system on the market that works completely without exhaust air.
This article first appeared on PROCESS on 19.10.2020.